监控立杆:
监控立杆也叫监控杆,分为八角监控杆,圆管监控杆,等径监控杆,变径监控杆,锥形监控杆,高度一般为3-6米,主要为交通道路,十字路口,学校,政府,小区,工厂,边防,机场等需要监控摄像的地方。监控立杆的使用提高了城市安全防范,是居民生活的有效保障。
1、没有特殊情况所有监控立杆预埋件混凝土为C25砼,所配钢筋符合国标及受风要求。其中水泥为425号普通硅酸盐水泥。混凝土的配比和**小水泥用量应符合GBJ204-83的规定;预埋件地脚螺栓法兰盘以上的螺纹包扎良好以防损坏螺纹。根据预埋件安装图正确放置监控立杆预埋件,****支臂杆的伸出。
2、监控立杆基础的混凝土浇注面平整度小于5mm/m尽量保持立杆预埋件水平。预埋件法兰盘低出周围地面20~30 mm ,再用C25细石砼把加强肋盖住,以防止积水。
1、杆旁、控制箱旁、电缆拐弯处、电缆管直线长度超过50米时或两端电缆管不在同一平面相距100 mm以上时,必须设置手孔井。
2、手孔井的内围尺寸要求为500(长)×500(宽)×600(深)MM,用砾石铺层作为渗水用;手孔井四壁必须抹水泥沙浆。
3、控制箱由设备厂家根据所需容量配备,外壳采用****冷轧钢板壁厚不小于1.2mm外表喷室外塑粉并做好防水防盗及散热。
4、结构用钢不得影响材料和机械性能的裂纹、分层、重皮、夹渣等缺陷麻点或划痕的深度不得大于钢材厚度负公差的1/2,且不应大于0.5mm。
5、设计依据:设计风载:23m/s2,疲劳寿命:30年,按国家**新标准版本《碳素结构钢》、《电气装置安装工程电缆线路施工及验收规范》、《钢结构工程施工及验收规范》、《钢筋混凝土工程施工验收规范》等相关规范进行施工。
6 制作要求
1、符合现行国家标准的规定,并有合格证明文件。碳素钢采用E43型焊条,焊条质量应符合**新国标的规定,绝不使用药皮脱落、焊芯生锈或受潮的焊条,以及带锈的焊丝。焊接尺寸符合设计要求,焊缝金属表面的焊波均匀,不得影响强度的裂纹、夹渣、焊瘤、烧穿、未溶合、弧坑和针状气孔,并且无褶皱和中断等缺陷。焊缝区咬肉深度不允许超过0.5mm,累计总长不得超过焊缝总长的10%。焊缝宽度小于20mm,焊角余高为1.5mm~2.5mm,角焊缝的焊角高度应为6mm~8mm,焊角尺寸不允许小于设计尺寸。
2、防腐处理采用热浸锌,在进行防腐处理前,应对钢构件进行有效的除锈,热浸锌厚度不小于85um,锌层应均匀,用硫酸铜液作浸蚀试验时,4次以上不露铁,锌层应与金属本体结合牢固,经锤击试验,锌层不剥离,不凸起。浸锌完毕后应进行钝化处理,并且48h盐雾试验合格。每100 m杆,其轴线测量的直线度误差不超过0.5‰,杆全长直线误差不超过1‰。
7 预埋件
1、基础的钢筋笼应临时固定,同时确保钢筋宠的基础顶板平面水平,即用水平尺在基础顶板垂直两个方向测量,观察其气泡必须居中;监控立杆预埋件基础混凝土浇捣必须密实,禁止混凝土有空鼓;
2、施工时要在预埋管口预先用塑料纸或其它材料封口,以防止混凝土时混凝土漏入预埋管中,造成预埋管堵塞;基础浇捣后,基础面必须要高于地平5MM-10MM;混凝土必须要养护一段时间,以确保混凝土能达到一定的安装强度。
3、每一根金属立杆都必须接地,其接地电阻小于4欧;各立杆基础具体数据视现场施工需要为准。
8 路口窨井
1、道路监控立杆一般只要求使用小规格窨井,为了设备安装方便窨井宜设置在监控杆附近;当地下水位不高时,窨井井底只铺砾石(沙子)垫层,以便雨天在窨井中积水渗入地下,但井壁下则须有混凝土基础垫层,井壁粉水泥沙浆;当地下水位很高时,窨井井底加一层10CM的混凝土垫层,井壁和井底要粉刷防水沙浆;
2、净尺寸500×500×600(长×宽×高),采用Mu10砖M5水泥沙浆240厚砌筑,盖板用Φ8@150双向配置C20砼预制板厚为60厚,标高同人行道面或绿化带,板面须光滑,设提孔,按国标制作盖板。各窨井土建具体数据视现场施工需要为准。
应用:柜内满足于计算机或工控设备的摆放
安装箱:满足19英寸桌面调音设备的安装
钣金产品注意事项:一是结构合理,二是强度,三是是否方便制作,四是美观度
要注意钣金的轧制方向,如果是单一的折一道弯的话,折弯线****与钣金的轧制方向垂直,这样可以避免钣金在折弯时出现断裂现象。如果是两个方向折弯时,应该把折弯的零件在落料时,**摆成45°的方向,这样可以避免任一方向的折弯出现断裂现象的发生。
钣金加工属于比较复杂的加工程序,太多的因素影响着钣金加工件的质量,完成加工之后的装配就是其中之一,岳搏精密机械专业钣金加工,如果装配过程中出现不合理的现象,那么钣金件的质量很可能因此受到影响。在装配前我们需要了解工件的相关资料..
1)分析研究产品的装配图和零件图。
(2)确定毛坯。
(3)拟定工艺路线,选择定位基面。
(4)确定各工序所采用的设备。
(5)确定各工序所采用的刀具、夹具、量具和辅助工具。
(6)确定各主要工序的技术要求及检验方法。
(7)确定各工序的加工余量,计算工序尺寸和公差。
(8)确定切削用量。
(9)确定工时定额。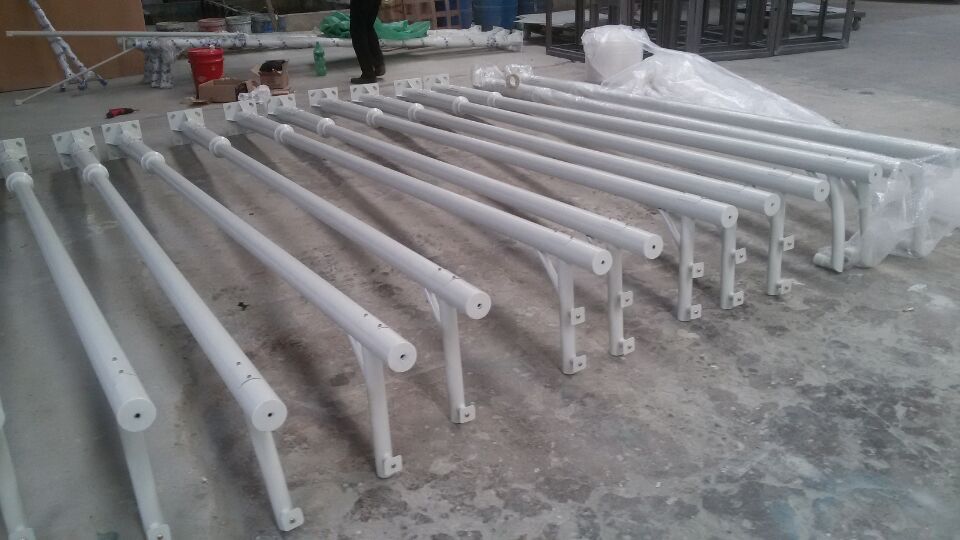